3D Printing industry
Three-dimensional (3D) printing, also known as additive manufacturing, is a rapidly growing market, valued at $17.4B, and projected to increase at a compound annual growth rate of ~20% over the next decade. A specialized 3D printing filament is required for operation, with a market value of $739 million in 2020, projected to pass $2.6 billion by 2025. While 3D printing is commonly used in manufacturing and architecture to quickly construct models and prototypes, it generates significant filament waste, with a high scrap rate of 30-50% in 2021. This resulted in approximately 5,000 tons of waste from 18,500 tons of plastic consumption in 2020.
To address this issue, RockyTech has developed engineered 3D printing filaments made from 100% recycled materials, providing a sustainable and cost-effective solution to support the growth of the 3D printing industry. By using recycled plastic filament, 3D printing companies can reduce their waste and environmental impact while also saving on material costs. As the market for 3D printing continues to expand and becomes more accessible, the need for sustainable and efficient production processes will only increase. RockyTech’s recycled filament offers a practical and eco-friendly solution to help the industry meet this demand.
Prosthetic industry
Plastic and composite materials are commonly utilized in the prosthetic industry as socket materials for various types of prosthetic devices, such as lower limb prostheses, upper limb prostheses, and spinal orthoses. The socket is the critical interface between the residual limb and the prosthetic device, and it plays a crucial role in the overall functionality and comfort of the device. At RockyTechâ„¢, we collaborate with Quorum Prosthetics to research and develop better material options for prosthetic sockets and liners that provide improved comfort and cost savings for amputees.
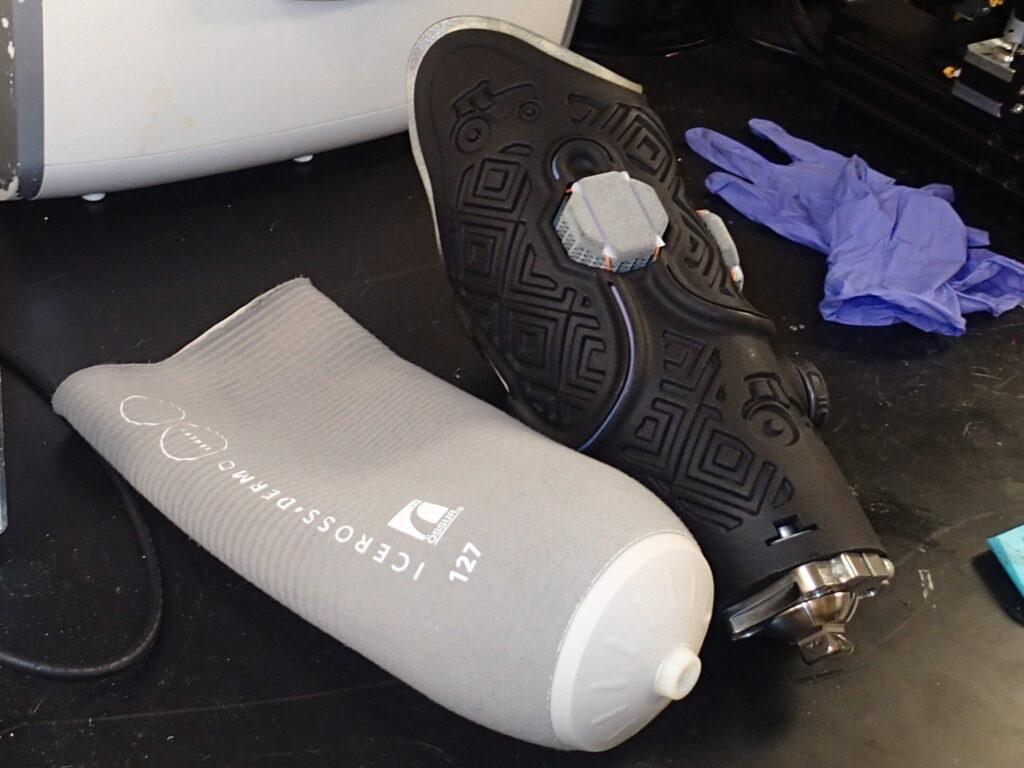
Consumer electronics
The consumer electronics market includes a wide range of products such as smartphones, laptops, TVs, home appliances, and wearable devices. These products are often made with plastic due to its lightweight, durability, and cost-effectiveness. The plastic market for consumer electronics was worth $5.7 billion in 2020 and is expected to reach $8.7 billion by 2027. Despite this growth, the industry is under increasing pressure to reduce plastic waste and become more sustainable. To address this, companies are exploring alternative materials such as bioplastics and recycled plastics, and implementing environmentally friendly practices throughout the supply chain. RockyTechâ„¢ joins this effort by providing upcycled plastics to improve circularity in the consumer electronics industry and increase the amount of recycled content in products. This approach aligns with the industry’s growing focus on sustainability and environmentally friendly practices. Additionally, upcycling can provide cost savings for companies by reducing the need for virgin materials and minimizing waste disposal costs.
Automobile industry
Carbon fiber composites (CFRPs) are increasingly used in the automobile industry due to their high strength-to-weight ratio and durability. By replacing traditional materials such as steel with CFRPs, the weight of an automobile body system can be reduced by over 20%, resulting in a 12-16% increase in fuel economy according to the Department of Energy (DOE). This translates to significant cost savings for car owners in the long run. However, the high cost of CFRPs has been a deterrent to their wide adoption in the mainstream market. To address this challenge, RockyTechâ„¢ has developed reprocessible and recyclable CFRPs using a proprietary covalent adaptable network as a matrix. This technology reduces the production time and cost of CFRPs, and also improves the circularity of CFRPs by enabling 100% recycling of both carbon fibers and chemical components. The use of such CFRPs helps to improve the cost and environmental footprint of these composites, making lightweight strategies more affordable for mainstream vehicles.